1、引言
【乐虎集团的官方网站
】金属叠片联轴器广泛应用在航空、舰船、石油化工、机械制造等各个领域,叠片联轴器为旋转机械提供一种高可靠性的联接方式,用来将原动机所产生的扭矩和旋转运动传递给从动机,补偿轴的不对中。
叠片联轴器工作时膜片与法兰交替连接产生挠性,膜片组上的扭矩是依靠螺栓圆上两相邻螺栓间切线方向传递,传扭时主动螺栓通过膜片牵动从动螺栓一起旋转,螺栓受剪力,膜片受拉力或压力。故而螺栓作为联轴器中不可缺少的零件对设备安全、项目工期和投资都有相当大的影响,不夸张的讲,设备中一个小小的螺栓断裂或腐蚀极有可能影响整个机组的寿命。
实际使用过程中螺栓损坏是z*常见的联轴器故障情况之一,其导致联轴器螺栓损坏的原因很多,本文通过典型案例从选型、安装等方面分析螺栓损坏的原因,以期在后期使用中避免此类问题的产生,寻找联轴器安全、长寿使用的有限方法。
2、案例描述
2014年,某项目2号机组10KIC触发SRI704KA (闭路冷却水泵公共出口管线压力低),2SRI系统流量由3610m3/h降至2546m3/h,2SRI201PO电流由21.63A下降至5.91A。2SRI301PO自动联启,联启后SRI704KA恢复,随后主控手动停运2SRI201PO。维修过程中将联轴器断开后,发现联轴器连接螺栓(共6根)均已断裂,叠片组件也已断裂,断裂螺栓和损坏的膜片见图1。
2014年05月客户邮件告知,该项目1号机组联轴器螺栓亦发生相同情况的断裂,联轴器型号均为TD6-**。
本文作者应用户要求,协助泵厂家查找原因。与现场技术人员沟通后得如下信息:TD6-**联轴器使用场合为电机驱动泵机组,功率220kW,转速1450rpm。该联轴器使用2年多,出现了螺栓和膜片组件断裂的情况。
3、故障原因分析
造成联轴器螺栓损坏的原因主要有以下几点:联轴器选型与结构是否合理,螺栓材质是否合适,联轴器安装是否正确等。接下来我们就来具体分析下:
3.1 联轴器选型与结构是否合理
叠片挠性联轴器选用一般以所需传递的计算扭矩小于联轴器的公称扭矩为原则。由于主动机的工作状况各不相同,所以在计算时需考虑工况系数K,见表1工况系数K值表(出自无锡创明联轴器样本)。
联轴器扭矩计算:T=9549×P×K/n
式中:T—扭矩(N.m)
p—主动机额定功率(kW)
K—工况系数
n—额定工作转速(r/min)
该项目联轴器使用场合为电机驱动泵机组,功率220kW,转速1450rpm。通过上述公式反计算实际工况系数得K=3.1。
这两个项目均为核电项目,根据我公司相关规范(核电联轴器/单膜片选型系数必须大于2.5),可得出此项目选TD6-470型联轴器能满足项目工况。
该项目联轴器两侧为电机和泵,轴头距离为24mm,当时设计联轴器图纸时,客户手成套设计条件所限要求采用单膜片联轴器。虽然通过上述工况系数的计算核实了TD6-470型号联轴器能满足该项目的系数要求,但从联轴器使用场合上看,该项目选用单膜片联轴器是不合适的,原因如下:
单膜片联轴器适用于连接的设备中有一根轴(主动机轴或从动机轴)是浮动的、只有单个支撑的场合,此时单膜片联轴器实际上起到了径向支撑的功能。典型应用场合示意图如图3及图4。

另外,在某些特殊设计的轴系如舰船推进系统、飞机的传动系统中也会应用到单膜片联轴器,它们采用单膜片联轴器的原理与上图类似。
根据该项目现场情况分析,此项目设备(电机-泵)而言,主、从动机主轴都是通过自身的二个轴承或轴瓦来径向支撑固定的,在这种场合下,使用单膜片联轴器从原理上来说都是不合适的。
从图5中可以看出,当使用单膜片(无中间节,L=0)的联轴器时,联轴器不具备补偿二轴径向不对中的能力。一旦机组在安装或运行过程中存在或产生较大的径向不对中,整个轴系会产生很大的弯曲应力和附加弯矩,从而导致:轴系振动超标;联轴器螺栓断裂;轴承、轴瓦、机封损坏;甚至主轴弯曲变形等故障。多年来我们在用户现场接触到很多这样的故障实例。
该项目联轴器的选用前期是由于客户意愿选择了单膜片联轴器,现场安装时必须满足以下苛刻的条件:
1、联轴器安装找正时,径向对中精度应符合要求:径向对中偏差不能超过0.1mm,对于较小型号的联轴器,径向偏差不超过0.05mm。
2、对机组的使用环境、运行状态有充分了解和把握,能够保证机组在长期运行时不会产生较大的径向不对中。然而事实上,在使用现场往往存在很多因素会导致径向不对中的产生:如基础沉降、地脚螺栓松动、机组热膨胀、管路的压差和膨胀以及很多事先无法完全预料的因素,因此要保证长期运行不产生较大不对中往往是很难做到的。
在该项目现场,我们就发现联轴器的安装对中偏差较大。这极有可能是造成该项目联轴器螺栓断裂的重要原因。对此我公司建议z*终客户将其更改为双膜片联轴器,保证了膜片联轴器的补偿性能,而且也方便泵的检、维修。
3.2 联轴器螺栓断裂是否正常
从用户提供的螺栓和膜片组件断裂照片(如图6所示)可以看出:螺栓断口位于螺纹收尾处,即螺栓光杆段与螺纹的交界处,而非螺栓承力的剪切面,可以判断螺栓不是由于扭矩载荷引起的断裂。
由于螺栓规格M12*1.5的限制,成品螺栓不具备制作标准拉伸试样,无法进行拉伸试验。故将现场断裂的螺栓委托第三方上海材料研究所检测中心进行分析。详情如下:
观察断裂螺栓的宏观形貌及断口宏观形貌(见图7),断裂面整体上颜色灰暗,且存在大面积擦伤,断口部分区域与轴向垂直。
将断口采用超声波清洗仪充分清洗后置于Quanta400FEG扫描电子显微镜(SEM)下观察,断口SEM低倍形貌见(见图8)
断口上的部分区域与轴向垂直,整个断口擦伤严重,部分区域异物覆盖,无法观察细微特征(见图9)
部分断口区域观察到韧窝特征,见图10。
少部分区域观察到疲劳特征,具有大致平行的二次裂纹和少量疲劳辉纹,见图11。
根据上述图片,断口上的大部分区域与轴向垂直,整个断口擦伤严重,部分区域观察到疲劳特征,具有大致平行的二次裂纹和少量疲劳辉纹,少部分区域观察到韧窝特征。分析结论是该断裂螺栓为疲劳断裂。
3.3联轴器螺栓受力是否超额
该项目现场螺栓发生断裂后,根据客户提供的图纸和现场人员的描述,我们发现客户现场螺栓出现反装的情况(现场错误安装),螺栓未按照设计图和使用说明书要求安装,安装方向反了,螺栓先穿过衬套,再穿入膜片组件和法兰,螺母压在法兰上。螺栓正确的安装方向应该从法兰向膜片组件穿,螺母应压在衬套上。错误的安装降低了螺纹与光杆段交界处的应力,特别是在机组出现不对中的情况下。在有不对中的条件下,螺栓反穿会恶化其受力状态,螺栓的螺纹段要承受额外的弯矩载荷(如图12、图13所示)。
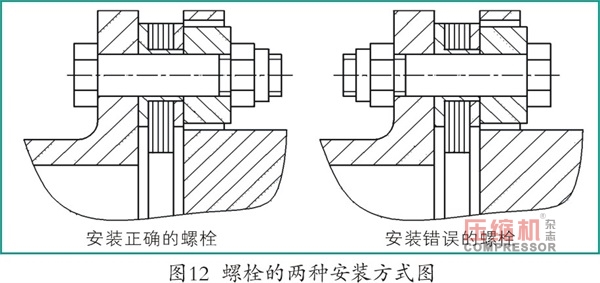
根据现场了解的情况,该项目机组情况:电机-泵,功率:220kW,转速:1450r/min,TD6-470型联轴器额定扭矩:4500Nm。通过公式我们可以看到,两者的剪切应力τ(τ=4TC/(πk1R1d2))、光杆段拉伸应力σt(σt =F0/As1)、螺栓复合载荷当量应力。
螺栓螺纹危险截面拉伸应力σtc (σt=F0/As2) ,这些应力值在两种安装方式下均相同,通过计算得均小于对应的许用应力。
所以,我们主要通过比较螺栓从法兰侧穿入和螺栓从片组侧穿入两种情况下挤压应力的大小来进行分析。
通过右表中螺栓校核计算结果比较,联轴器TD6-**的螺栓材料采用42CrMo时满足应力要求,螺栓的设计足够安全,但是合理安装时,螺栓承力段长度为整个法兰边的厚度,而如果将螺栓反过来穿,则螺栓承力段长度将会缩短(如图12所示)。
承力段的长度决定了传扭孔与螺栓光杆配合部位的应力和法兰边孔口挤压应力的大小,承力段长度越长则应力越小,反之承力段越短则应力越大。
4、结论
根据我公司有关质量记录和上海材料研究所检测中心的分析报告可以确定,该联轴器的螺栓不存在原材料和热处理方面的缺陷。
结合强度计算和故障现象分析,我们认为该联轴器螺栓的断裂是由于过大的不对中载荷的持续作用和螺栓不正确的安装导致。
用户安装时需对机组驱、从动机进行检查并重新对中找正,正确安装螺栓并按规定力矩拧紧螺母,而且要采取措施保证机组的不对中在运行过程中不超出联轴器设计许用范围。联轴器安装时要严格按照说明书进行安装,包括机组对中、螺栓装配方向、螺母拧紧力矩等。机组也需要进行定期检修、保养,以及时排除故障,延长设备的寿命。
条件允许的话应立刻更换成双膜片联轴器,从根本上解决原联轴器的结构缺陷。同时在后期选型时明确在重要场合中避免采用单膜片联轴器,因为只有合适的联轴器结构才能充分发挥叠片联轴器独特的优势,保障机组平稳运行,为装置的安全生产保驾护航。
参考文献
[1] [机械设计手册第四版],化学工业出版社
[2] [中国机械工业标准汇编第二版],中国标准出版社
[3] [理论力学第六版],高等教育出版社
[4] 中广核会议手册,20140915
[5] 单片组联轴器的缺陷及使用场合
[6] 上海材料研究所检测中心螺栓分析报告
1、引言
【乐虎集团的官方网站
】金属叠片联轴器广泛应用在航空、舰船、石油化工、机械制造等各个领域,叠片联轴器为旋转机械提供一种高可靠性的联接方式,用来将原动机所产生的扭矩和旋转运动传递给从动机,补偿轴的不对中。
叠片联轴器工作时膜片与法兰交替连接产生挠性,膜片组上的扭矩是依靠螺栓圆上两相邻螺栓间切线方向传递,传扭时主动螺栓通过膜片牵动从动螺栓一起旋转,螺栓受剪力,膜片受拉力或压力。故而螺栓作为联轴器中不可缺少的零件对设备安全、项目工期和投资都有相当大的影响,不夸张的讲,设备中一个小小的螺栓断裂或腐蚀极有可能影响整个机组的寿命。
实际使用过程中螺栓损坏是z*常见的联轴器故障情况之一,其导致联轴器螺栓损坏的原因很多,本文通过典型案例从选型、安装等方面分析螺栓损坏的原因,以期在后期使用中避免此类问题的产生,寻找联轴器安全、长寿使用的有限方法。
2、案例描述
2014年,某项目2号机组10KIC触发SRI704KA (闭路冷却水泵公共出口管线压力低),2SRI系统流量由3610m3/h降至2546m3/h,2SRI201PO电流由21.63A下降至5.91A。2SRI301PO自动联启,联启后SRI704KA恢复,随后主控手动停运2SRI201PO。维修过程中将联轴器断开后,发现联轴器连接螺栓(共6根)均已断裂,叠片组件也已断裂,断裂螺栓和损坏的膜片见图1。

2014年05月客户邮件告知,该项目1号机组联轴器螺栓亦发生相同情况的断裂,联轴器型号均为TD6-**。
本文作者应用户要求,协助泵厂家查找原因。与现场技术人员沟通后得如下信息:TD6-**联轴器使用场合为电机驱动泵机组,功率220kW,转速1450rpm。该联轴器使用2年多,出现了螺栓和膜片组件断裂的情况。
3、故障原因分析
造成联轴器螺栓损坏的原因主要有以下几点:联轴器选型与结构是否合理,螺栓材质是否合适,联轴器安装是否正确等。接下来我们就来具体分析下:
3.1 联轴器选型与结构是否合理
叠片挠性联轴器选用一般以所需传递的计算扭矩小于联轴器的公称扭矩为原则。由于主动机的工作状况各不相同,所以在计算时需考虑工况系数K,见表1工况系数K值表(出自无锡创明联轴器样本)。
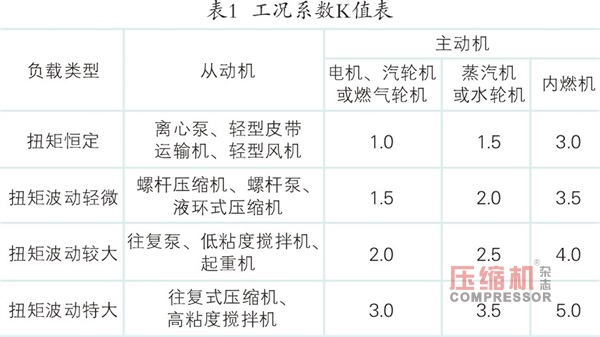
联轴器扭矩计算:T=9549×P×K/n
式中:T—扭矩(N.m)
p—主动机额定功率(kW)
K—工况系数
n—额定工作转速(r/min)
该项目联轴器使用场合为电机驱动泵机组,功率220kW,转速1450rpm。通过上述公式反计算实际工况系数得K=3.1。
这两个项目均为核电项目,根据我公司相关规范(核电联轴器/单膜片选型系数必须大于2.5),可得出此项目选TD6-470型联轴器能满足项目工况。
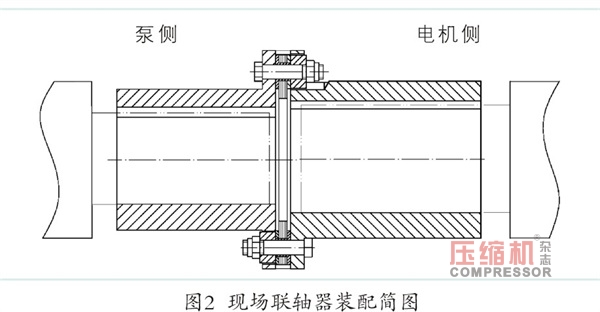
该项目联轴器两侧为电机和泵,轴头距离为24mm,当时设计联轴器图纸时,客户手成套设计条件所限要求采用单膜片联轴器。虽然通过上述工况系数的计算核实了TD6-470型号联轴器能满足该项目的系数要求,但从联轴器使用场合上看,该项目选用单膜片联轴器是不合适的,原因如下:
单膜片联轴器适用于连接的设备中有一根轴(主动机轴或从动机轴)是浮动的、只有单个支撑的场合,此时单膜片联轴器实际上起到了径向支撑的功能。典型应用场合示意图如图3及图4。

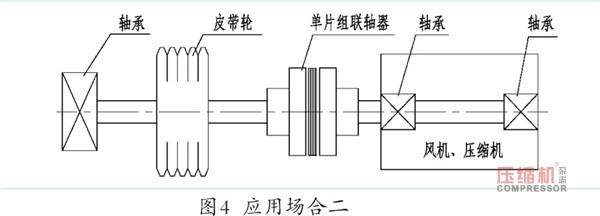
另外,在某些特殊设计的轴系如舰船推进系统、飞机的传动系统中也会应用到单膜片联轴器,它们采用单膜片联轴器的原理与上图类似。
根据该项目现场情况分析,此项目设备(电机-泵)而言,主、从动机主轴都是通过自身的二个轴承或轴瓦来径向支撑固定的,在这种场合下,使用单膜片联轴器从原理上来说都是不合适的。
从图5中可以看出,当使用单膜片(无中间节,L=0)的联轴器时,联轴器不具备补偿二轴径向不对中的能力。一旦机组在安装或运行过程中存在或产生较大的径向不对中,整个轴系会产生很大的弯曲应力和附加弯矩,从而导致:轴系振动超标;联轴器螺栓断裂;轴承、轴瓦、机封损坏;甚至主轴弯曲变形等故障。多年来我们在用户现场接触到很多这样的故障实例。
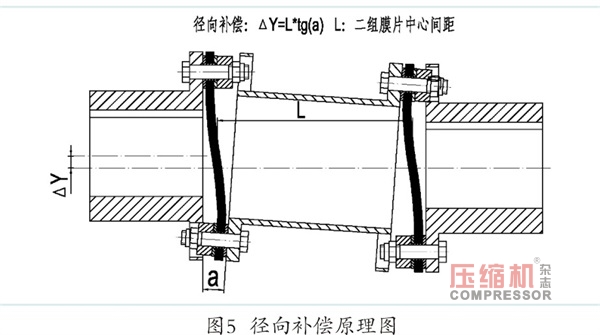
该项目联轴器的选用前期是由于客户意愿选择了单膜片联轴器,现场安装时必须满足以下苛刻的条件:
1、联轴器安装找正时,径向对中精度应符合要求:径向对中偏差不能超过0.1mm,对于较小型号的联轴器,径向偏差不超过0.05mm。
2、对机组的使用环境、运行状态有充分了解和把握,能够保证机组在长期运行时不会产生较大的径向不对中。然而事实上,在使用现场往往存在很多因素会导致径向不对中的产生:如基础沉降、地脚螺栓松动、机组热膨胀、管路的压差和膨胀以及很多事先无法完全预料的因素,因此要保证长期运行不产生较大不对中往往是很难做到的。
在该项目现场,我们就发现联轴器的安装对中偏差较大。这极有可能是造成该项目联轴器螺栓断裂的重要原因。对此我公司建议z*终客户将其更改为双膜片联轴器,保证了膜片联轴器的补偿性能,而且也方便泵的检、维修。
3.2 联轴器螺栓断裂是否正常
从用户提供的螺栓和膜片组件断裂照片(如图6所示)可以看出:螺栓断口位于螺纹收尾处,即螺栓光杆段与螺纹的交界处,而非螺栓承力的剪切面,可以判断螺栓不是由于扭矩载荷引起的断裂。

由于螺栓规格M12*1.5的限制,成品螺栓不具备制作标准拉伸试样,无法进行拉伸试验。故将现场断裂的螺栓委托第三方上海材料研究所检测中心进行分析。详情如下:
观察断裂螺栓的宏观形貌及断口宏观形貌(见图7),断裂面整体上颜色灰暗,且存在大面积擦伤,断口部分区域与轴向垂直。

将断口采用超声波清洗仪充分清洗后置于Quanta400FEG扫描电子显微镜(SEM)下观察,断口SEM低倍形貌见(见图8)

断口上的部分区域与轴向垂直,整个断口擦伤严重,部分区域异物覆盖,无法观察细微特征(见图9)

部分断口区域观察到韧窝特征,见图10。

少部分区域观察到疲劳特征,具有大致平行的二次裂纹和少量疲劳辉纹,见图11。

根据上述图片,断口上的大部分区域与轴向垂直,整个断口擦伤严重,部分区域观察到疲劳特征,具有大致平行的二次裂纹和少量疲劳辉纹,少部分区域观察到韧窝特征。分析结论是该断裂螺栓为疲劳断裂。
3.3联轴器螺栓受力是否超额
该项目现场螺栓发生断裂后,根据客户提供的图纸和现场人员的描述,我们发现客户现场螺栓出现反装的情况(现场错误安装),螺栓未按照设计图和使用说明书要求安装,安装方向反了,螺栓先穿过衬套,再穿入膜片组件和法兰,螺母压在法兰上。螺栓正确的安装方向应该从法兰向膜片组件穿,螺母应压在衬套上。错误的安装降低了螺纹与光杆段交界处的应力,特别是在机组出现不对中的情况下。在有不对中的条件下,螺栓反穿会恶化其受力状态,螺栓的螺纹段要承受额外的弯矩载荷(如图12、图13所示)。
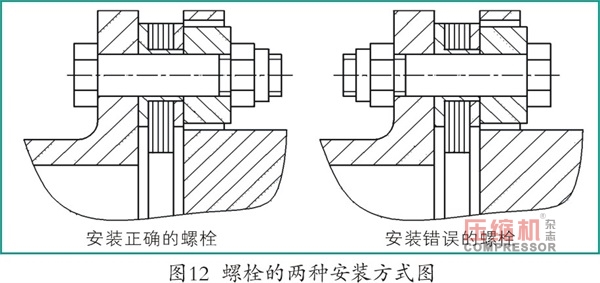
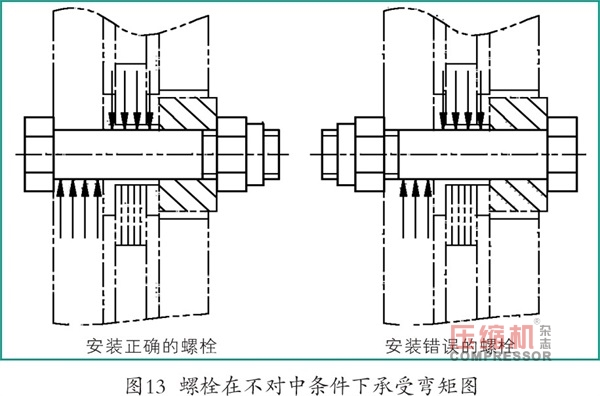
根据现场了解的情况,该项目机组情况:电机-泵,功率:220kW,转速:1450r/min,TD6-470型联轴器额定扭矩:4500Nm。通过公式我们可以看到,两者的剪切应力τ(τ=4TC/(πk1R1d2))、光杆段拉伸应力σt(σt =F0/As1)、螺栓复合载荷当量应力。
螺栓螺纹危险截面拉伸应力σtc (σt=F0/As2) ,这些应力值在两种安装方式下均相同,通过计算得均小于对应的许用应力。
所以,我们主要通过比较螺栓从法兰侧穿入和螺栓从片组侧穿入两种情况下挤压应力的大小来进行分析。
通过右表中螺栓校核计算结果比较,联轴器TD6-**的螺栓材料采用42CrMo时满足应力要求,螺栓的设计足够安全,但是合理安装时,螺栓承力段长度为整个法兰边的厚度,而如果将螺栓反过来穿,则螺栓承力段长度将会缩短(如图12所示)。
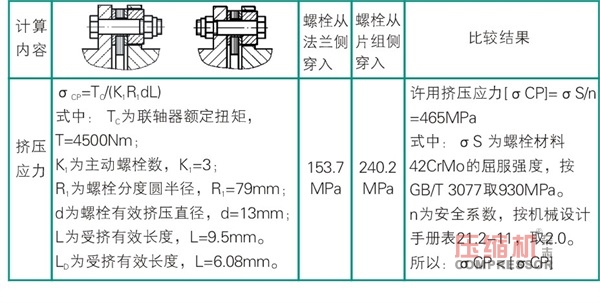
承力段的长度决定了传扭孔与螺栓光杆配合部位的应力和法兰边孔口挤压应力的大小,承力段长度越长则应力越小,反之承力段越短则应力越大。
4、结论
根据我公司有关质量记录和上海材料研究所检测中心的分析报告可以确定,该联轴器的螺栓不存在原材料和热处理方面的缺陷。
结合强度计算和故障现象分析,我们认为该联轴器螺栓的断裂是由于过大的不对中载荷的持续作用和螺栓不正确的安装导致。
用户安装时需对机组驱、从动机进行检查并重新对中找正,正确安装螺栓并按规定力矩拧紧螺母,而且要采取措施保证机组的不对中在运行过程中不超出联轴器设计许用范围。联轴器安装时要严格按照说明书进行安装,包括机组对中、螺栓装配方向、螺母拧紧力矩等。机组也需要进行定期检修、保养,以及时排除故障,延长设备的寿命。
条件允许的话应立刻更换成双膜片联轴器,从根本上解决原联轴器的结构缺陷。同时在后期选型时明确在重要场合中避免采用单膜片联轴器,因为只有合适的联轴器结构才能充分发挥叠片联轴器独特的优势,保障机组平稳运行,为装置的安全生产保驾护航。
参考文献
[1] [机械设计手册第四版],化学工业出版社
[2] [中国机械工业标准汇编第二版],中国标准出版社
[3] [理论力学第六版],高等教育出版社
[4] 中广核会议手册,20140915
[5] 单片组联轴器的缺陷及使用场合
[6] 上海材料研究所检测中心螺栓分析报告
网友评论
条评论
最新评论